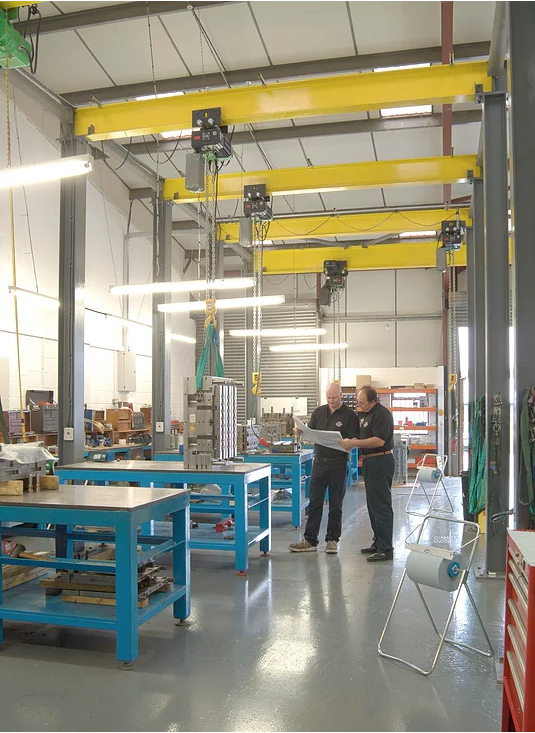
Based in Totnes, Devon, Amtek is one of the UK’s foremost toolmakers specialising in plastic injection mould tools and high precision CNC machined components. At its 21,000 ft2 facility the company has invested in it is ability to ‘go large’.
High precision multi-cavity caps and closures injection mould tools and complex CNC components are the mainstays for the highly skilled engineering team at Amtek. The company’s impressive plant list includes a high accuracy Mikron HSM 400 machining centre with robotic pallet loader, a Mikron 65,000 rpm Graphite Master machining centre also with a robotic pallet loader that has allowed Amtek to switch from copper to predominantly graphite EDM electrodes for its die sink machines, and a Mazak Integrex multi-axis mill-turn centre.
Most often a fully assembled plastic injection mould tool might weigh up to 5 tonnes. The team at Amtek took the decision that this was not enough and invested in material handling solutions capable of safely moving the mould tool component parts each weighing up to 8 tonnes around its workshop and finishing/assembly area.
“It means we can extend the number of cavities within the tool for our customers,” explains Production Manager, Mike Lawes. “Typically, for the injection moulded caps and closures that we are renowned for a 5 tonne tool would have 96 impressions. Thanks to our material handling and well-planned workflow through our entire facility, from receipt of the raw material right through to inspection and dispatch, we can offer larger tools with up to 128 impressions.”
That 33 per cent increase can make a significant difference to the mould customer, as Mike Lawes points out: “The cycle time for the tool might be around 6 seconds, which equates to around 1 million cycles per year. The additional tool capacity could result in an extra 33 million parts being produced.”
Even with the increase in the number of injected components that can be produced the same rigorous toolmaking systems and methods are applied. Tool longevity is vital to Amtek’s customers so it becomes second nature to the company’s highly skilled staff to check and recheck everything. “We have tools in the market that have completed more than 30 million cycles, you don’t achieve that level of reliability by accident, you have to add quality at every step of the mould tools creation,” he adds.